供應商質量管理(Supplier Quality Management ,簡稱SQM),是把被動的來料質量控制(IQC)轉變為更加主動的全面供應商質量管理系統。
其目的是維持和提高供應商的品質保證能力,以持續提供符合或超越質量要求的產品。

供應商質量管理核心任務包括新供應商的導入、產品(零部件)實現、批量生產績效管理三個環節 (如下圖所示)。
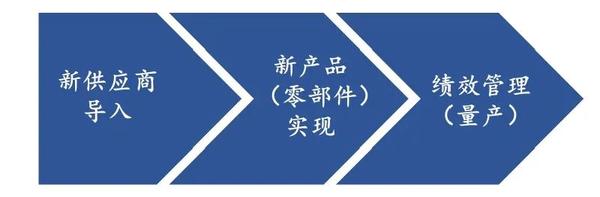
圖:供應商質量管理核心任務
關于新供應商導入環節質量如何管理,新產品(零部件)實現過程供應商的質量管理,以及批量生產階段供應商質量的管理,將在以后的文章中分析闡述。
SQM供應商質量管理
在質量管理框架中的作用
SQM 供應商質量管理是質量管理中非常重要的一環。
對于很多制造業的企業來講,原材料成本占銷售成本的50%以上。在某些零部件生產行業這個占比可能會達到60%,甚至更高。
原材料質量直接影響到公司整體成本,且供應商質量管理水平的高低,很大程度上影響整個公司的質量管理水平,影響著企業競爭力,當然也影響著供應商自身的競爭力。
如何識別企業自身的供應商管理水平呢?我們沿用質量管理4.0的理論,分析自身供應商管理系統,定位處于質量管理的階段,為供應商質量管理奠定提升路徑圖。
1. 供應商質量管理1.0 ,典型特點“無”
無專職的供應商質量管理人員,在供應商導入時往往以采購、價格主導,質量系統流于形式或者缺失;
產品開發過程管理基本是“零”;供應商的質量保證全靠來料質量控制(IQC)進行攔截,每天只能祈禱供應商不要犯錯;
來料不良處理簡單粗暴,沒有形成原因分析及改善機制,周而復始,一直走不出惡性循環的圈兒。
一言以蔽之,處于這個階段的企業,因為沒有專職的供應商質量管理人員,所以在供應商導入的過程中沒有選好有能力的供應商;
因為沒有專職的供應商質量管理人員,所以在供應商零部件開發過程中不能消除潛在的質量風險;
因為沒有專職的供應商質量管理人員,在供應商零部件產生投訴以后不能有效跟蹤改善驗證的結果;
因為沒有專門的供應商質量管理人員,客戶投訴一旦跟原材料有關便不能及時的從供應商處得到改善的措施,從而引起客戶的不滿。
2. 供應商質量管理2.0 ,典型特點“查”
處于供應商質量管理2.0階段的企業,已經開始設置專職的SQE(Supplier Quality Engineer 供應商質量工程師)。
SQE 在供應商導入、零部件開發、量產管理中開始拋頭露面,但其主要的手段是以Audit (審核)為主。
每次到供應商處都會指出這不行,那不行,要求供應商提交的各種文件,也能挑出很多毛病,至于具體什么樣行,就不得而知了。
雖然供應商的績效也能給予反饋,但是怎么能改好,還是無從下手。一個字概括這個階段企業供應商質量管理的特點就是“審”,處于乙方的供應商通常是心服口不服。
3. 供應商質量管理3.0 ,典型特點“改”
處于供應商質量管理3.0階段的企業,其SQE除了能完成上述描述的各種審核與挑刺兒以外,其核心的任務是能幫助供應商找出到底是哪兒不行,甚至能夠通過DOE、CAPA、FMEA 等質量工具幫助供應商找出可行的解決方案。
但是仍停留在事后改善,也就是當供應商績效出現問題的時才會出擊去解決。
“改”字為主要特征的供應商質量管理已經開始憑借自己的專業性受到供應商的歡迎了。
4. 供應商質量管理4.0 ,典型特點“導”
處于供應商質量管理4.0階段的企業已經把供應商質量工程師SQE按工作內容拆分處SDE (Supplier Development Engineer 供應商發展工程師)和SQAE (Supplier Quality Assurance Engineer供應商質量保證工程師)。
其中SDE負責供應商導入跟供應商零部件的實現兩個核心任務,SQAE 負責供應商量產供貨績效的管控。
分工的細化,使得SDE能從日常紛雜的救火當中脫離出來,全身心專注于前期的策劃工作,在供應商犯錯之前,就通過輔導供應商在策劃過程中貫徹落實“一次做對”,從而最大程度上減少量產以后質量問題的產生。
即便是有漏網之魚,量產過程中SQAE及時的跟進也會保證供應商質量問題的改善得以即使落實。
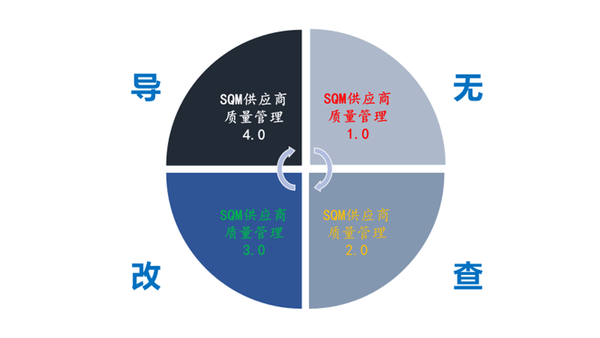
圖:SQM供應商管理在質量管理中的作用
在不同的發展階段,供應商質量管理SQM對公司質量的貢獻也不一樣。發展階段越高,供應商質量管理對整體質量管理的貢獻也就越大。
4.0階段,尤其是專注于供應商前期開發質量管控的SDE的出現,將會在提升供應商質量保證能力的同時有效為企業整體質量水平的提升打好基礎