一、什么是FMEA
FMEA:潛在失效模式與效應分析,全稱Potential Failure mode and effects analysis 。最早是由美國國家宇航局(NASA)形成的一套分析模式,FMEA是一種實用的解決問題的方法,可適用于許多工程領域,世界許多汽車生產商和電子制造服務商(EMS)都已經采用這種模式進行設計和生產過程管理和監(jiān)控。FMEA是一種試錯的思維模式,可以理解為給一個清單,告訴可能會犯的錯,以及錯誤的結果和嚴重性。當面對一個陌生的概念或領域時,有個東西,用來引導,消除陌生,避免因此可能導致的問題發(fā)生。這個東西就是FMEA。
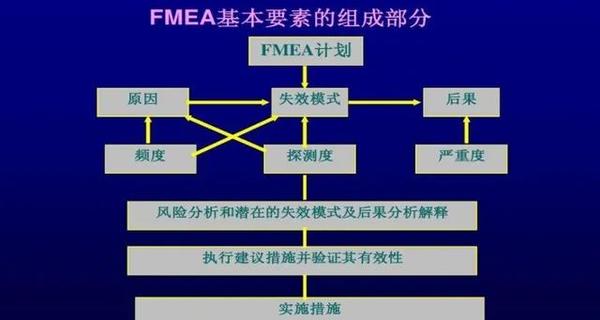
二、FMEA的分類
FMEA通常分為三類:
1.SFMEA(系統(tǒng)失效模式及后果分析):1.將研究的系統(tǒng)結構化,并分成系統(tǒng)單元,說明各單元間的功能關系。2.從已描述的功能中導出每一系統(tǒng)單元的可想象的失效功能(潛在缺陷)。3.確定不同系統(tǒng)單元失效功能間的邏輯關系,以便能在系統(tǒng)FMEA中分析潛在的缺陷、缺陷后果和缺陷原因
2.DFMEA(設計失效模式及后果分析):在設計和制造產品時,FMEA是一種可靠性設計的重要方法。它實際上是FMA(故障模式分析)和FEA(故障影響分析)的組合。它對各種可能的風險進行評價、分析,以便在現有技術的基礎上消除這些風險或將這些風險減小到可接受的水平。及時性是成功實施FMEA的最重要因素之一,它是一個“事前的行為”,而不是“事后的行為”。
3.PFMEA(過程失效模式及后果分析):是由負責制造/裝配的工程師/小組主要采用的一種分析技術,用以最大限度地保證各種潛在的失效模式及其相關的起因/機理已得到充分的考慮和論述。
三、FMEA分析流程
FMEA分析七步法:
步驟一:策劃和準備(定義范圍,使用了“5T's 、框圖、過程框圖”等來定義范圍)
步驟二:結構分析(結構分析,使用了“邊界圖、結構樹”等來進行結構分析)
步驟三:功能分析(使用了“P圖、功能樹、功能矩陣圖”等來進行功能分析)
步驟四:失效分析(使用了“FE-FM-FC表、失效網圖”等進行失效分析)
步驟五:風險分析(全新的嚴重度、頻度、探測度評分標準,取消了RPN,采用AP優(yōu)先級)
步驟六:優(yōu)化(確定降低風險的措施、職責、期限,及措施后的風險再評估)
步驟七:結果文件化(完成FMEA文件,向管理層、客戶、供應商溝通風險)
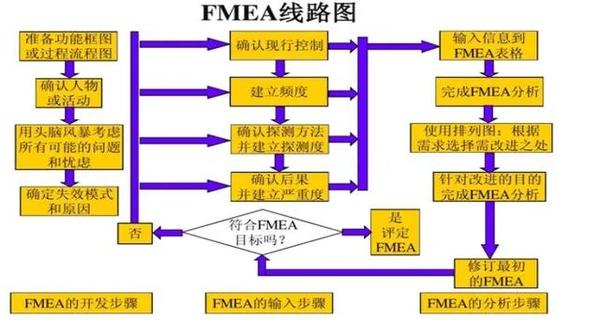
四、FMEA在設備中的應用
FMEA在設備管理中,可以進行設備故障風險預防,保障設備運行的可靠性。
1、用于設備維護計劃。制造工廠中設備維護計劃(EMP)的主要目的是最小化計劃外事件對安全,環(huán)境和業(yè)務盈利能力的影響。FMEA是實現和維持EMP目標的可靠工具。最佳的長期擁有成本通常是有效促進和徹底實施的FMEA的結果。
2、用于設備失效分析。針對設備運行過程及設備停機狀態(tài)中的失效模式進行分析,確定失效后果,失效原因,預防、探測手段,然后制定改善措施。
3、用于設備設計。采取科學合理的應用流程和方式來完善設備的實際設計,保證設備的質量,避免設備在實際的使用中出現各種問題。